Finis les exercices d’alerte, voici Vendor Managed Inventory
Personne ne peut réguler efficacement et durablement pour son propre profit tous les facteurs qui déterminent l’évolution économique. Les prévisions et les planifications ne sont pas des paramètres stables et sûrs pour la gestion d’une entreprise. C’est pourquoi la chaîne des fournisseurs, dans sa complexité et ses interdépendances, peut vaciller au moindre écart.
C’est pour cette raison que les professionnels de l’approvisionnement sont souvent contraints aux «exercices d’alerte». Ils doivent sauver ou décaler des dates, augmenter ou réduire des quantités à livrer et, en même temps, tranquilliser les clients et faire pression sur les fournisseurs. Cette liste pourrait être allongée à volonté. Le fait est que les acheteurs font face chaque jour à des surprises, ce qui leur laisse peu de temps pour optimiser la Supply Chain. Fournisseurs et clients envoient leurs opérateurs au combat (les supérieurs œuvrant souvent en arrière-plan) pour avoir le «dernier mot écrit». La confiance entre les partenaires est détruite, si tant est qu’elle ait existé un jour. L’aspiration à une réelle coopération reste un rêve parce que nous tournons comme des hamsters hébétés dans la roue de la frénésie opérationnelle. Dans ce «combat quotidien», il se développe entre les partenaires une culture du reproche et de la déception réciproques. La victoire revient au plus fort, c’est-à-dire à celui qui est en position dominante sur le marché.
Tendance à la concentration et à l’automatisation
Ne sous-estimons pas non plus la pression constante de la concurrence et des coûts, ni les tendances à la concentration et à l’automatisation qu’elle entraîne. Aucune entreprise ne devrait renoncer à optimiser ses processus d’approvisionnement et de logistique. La standardisation et l’automatisation demandent cependant que l’on soit prêt à évoluer et à investir. Les fabricants peuvent alors collaborer plus étroitement avec leurs partenaires et utiliser les avantages de la standardisation et de l’automatisation pour des procédures internes à l’entreprise.
Les entreprises focalisent toujours plus sur les processus de livraison et leurs structures car la valeur ajoutée externe représente aujourd’hui pour beaucoup d’entreprises de production une grande part des coûts globaux, quelquefois jusqu’à 70%. Ainsi, la compétitivité dépend dans une large mesure de la performance des fournisseurs et de l’Inbound Supply Chain conçue ensemble.
Essentiel pour la logistique
Le concept d’approvisionnement «Vendor Managed Inventory» se présente comme une stratégie efficace pour contrecarrer ces problèmes. L’«inventaire géré par le fournisseur» a été inventé aux USA au début des années 80. Il s’agit pour le fournisseur ou le fabricant de prendre sous sa tutelle les inventaires de ses clients. Pour ce faire, ces derniers lui communiquent des informations importantes relatives à la consommation et aux données prévisionnelles. Sur leur base, il établit ensuite ses propres pronostics et commandes.
La littérature spécialisée juge positivement le VMI qu’elle considère essentiel pour la logistique avec son concept de coopération orienté sur le rendement. Il existe toujours plus d’articles illustrés d’exemples pratiques qui thématisent l’utilité du VMI pour les partenaires et la disponibilité constante du matériel, ce qui représente une réduction des coûts sur l’ensemble de la Supply Chain et donc un avantage concurrentiel.
Avec le VMI et l’approvisionnement de sites de production et d’assemblage, les fournisseurs renforcent non seulement leur contrôle sur la chaine de livraison, mais utilisent aussi cette marge de manœuvre pour optimiser les lots de production et de transport. Un VMI performant rationnalise donc les processus d’achat et les effets se répercutent sur le rendement des partenaires.
Avantages et inconvénients
Le principal avantage du VMI est de permettre au fournisseur d’offrir un meilleur service au client. Pour les deux, le concept de VMI se prête idéalement au domaine de la maintenance. Des besoins irréguliers, peu de grandes fluctuations de la demande et la faible valeur des articles à acheter offrent les meilleures conditions pour l’implémentation d’une solution VMI. Dans ces positions relevant principalement du secteur partiel C, la procédure de commande simplifiée du VMI réduit fortement les coûts pour l’utilisateur. Du fait du nombre élevé de pièces de rechange et de maintenance.
La disparition de certaines étapes du processus est particulièrement importante ici – par exemple, le calcul permanent des besoins nets ou le traitement des propositions de commande, l’établissement ou la validation des commandes ou, le cas échéant, leur confirmation ou modification ainsi que les rappels au fournisseur.
De nouveaux chiffres-clés comme la comparaison des délais de livraison en fonction de la demande (l’ERP continue de tourner en arrière-plan) et les dates de livraison VMI permettent de vérifier continuellement la plausibilité des dispositions. La somme de tous les avis autorise une observation à court terme des liquidités par le client. Du fait de la fixation des minima et maxima, les inventaires sont mieux pronosticables en quantité et en valeur et diminuent d’autant chez le client et le fournisseur. L’effet coup de fouet (Bullwhip-Effect) dû aux variations trop forte de la demande est ainsi contrecarré.
La possibilité de planifier librement la production permet des délais de livraison plus courts et une meilleure flexibilité. La marge de manœuvre des dispositions réduit drastiquement le taux de retour et les transports spéciaux des fournisseurs. Mais, surtout, l’intense collaboration avec le fournisseur crée un climat de confiance: les problèmes trouvent une solution rapide et ouverte dans un esprit de partenariat.
Un instrument de controlling global est généré, le flux de quantité et de valeur est examiné conjointement. Résultat: une détection des erreurs simple et rapide, contrairement aux méthodes de commande traditionnelles avec leurs connexions complexes.
Les expériences faites par les utilisateurs de VMI confirment clairement dans la pratique les avantages cités. La coopération s’exprime par un partage du travail et une collaboration ciblée sur la base de valeurs, d’objectifs et d’intérêts communs.
Mais malgré ces avantages évidents le VMI reste peu répandu dans l’industrie. L’une des raisons en est le manque de confiance entre participants. Ainsi, par exemple, le transfert non filtré des données de disposition actuelles et des informations est d’emblée exclue. De plus, beaucoup d’entreprises y réfléchissent à deux fois avant de dévoiler leurs cartes à leurs fournisseurs alors que la confiance est essentielle pour la réussite du projet VMI. Et que dire de la réticence des acteurs à mettre à disposition leurs maigres ressources et investissements pour un projet «si peu connu»?
De par ses procédures orientées vers la consommation, le VMI se prête mal aux fortes fluctuations des besoins et aux productions spéciales. Dans l’impossibilité de rompre à court terme le «partenariat», le client devient vite dépendant du fournisseur ou du fabricant. Il est difficile d’«enthousiasmer» les sous-traitants et domaines internes du client car il n’est pas facile de les convaincre des bénéfices des procédures VMI. A cela s’ajoute la profonde mutation des processus opérationnels tant chez le client que le fournisseur. Sans parler des dépenses d’investissement générées par l’Internet et des mesures de sécurité qui doivent être développées et implémentées pour tous les systèmes et processus.
Application technologique
Pour une implémentation technologique en douceur du VMI, quelques étapes sont essentielles. Qu’elle soit basée sur un software ou sur Internet, une solution adéquate doit toujours permettre ceci:
- contrôle minutieux du transfert des données et de leur validité
- flexibilité au niveau des formats de données du client ou du fournisseur
- flexibilité au niveau des méthodes de transmission des données
- possibilité d’adaptation rapide en cas de changement du système commercial du client ou du fournisseur
Il y a ici deux approches fondamentales. Les solutions les plus courantes se basent sur les données planifiées constamment réajustées. Au niveau des stocks, les minima et maxima ne sont pas prioritaires et ne servent que de guides. Il s’agit donc toujours d’une forme de calcul des besoins nets.
Le VMI, au sens d’un contrôle de la consommation, se distingue essentiellement des outils habituels du marché. La compétence en matière de planification et gestion de l’inventaire est totalement déléguée au fournisseur. Les besoins permanents ne sont plus contrôlés par le client synchroniquement à la production et en fonction des besoins nets, mais seulement en fonction de la consommation et réglés par les minima et maxima de l’inventaire. Il n’y a pas d’informations du client au fournisseur si les variations de la planification restent dans la norme. Toutefois, la portée est constamment estimée à partir du ERP et indiquée en ligne au partenaire sur la base d’une planification annuelle pour les fournisseurs, dont seules les modifications importantes sont signalées par le client. Les minima et maxima sont calculés à partir de la taille du lot de production du client et des temps de livraison du fournisseur. Cette solution VMI permet de gérer aussi bien les articles A - B que C.
Conclusion philosophique
L’utilité du VMI ne se mesure pas exclusivement à des effets quantitatifs à court et moyen terme comme l’augmentation du chiffre d’affaires ou la réduction des coûts. Le VMI conduit à un changement radical de philosophie et se distingue surtout par la relation de confiance entre les partenaires dans un esprit de coopération. Du côté du client, l’achat assume un nouveau rôle: moins «bureau des commandes opérationnel» et plus «concepteur et optimiseur de la chaîne logistique»
Horst Bayer
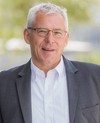
L’auteur est partenaire et l’«œil de l’achat» dans le cabinet de conseil «Peter Schreiber & Partner» à Ilsfeld bei Heilbronn. Gestionnaire d’entreprise de formation et plus de 30 ans expert en gestion des matières, achat et logistique, il a été récemment 10 ans chef de l’achat et de la logistique d’un sous-traitant automobile pour les pièces métalliques et les assemblages. Dans cette fonction, Horst Bayer a développé avec une entreprise de logiciels un outil VMI «radicalement simplifié».